Fluid Energy provides a great variety of blending services and capabilities for dry powders. Fluid Energy has both pilot and production size ribbon and paddle blenders to handle the most precise dry blending requirements. These blenders range in size from 14 to 200 cubic feet. Fluid Energy engineers and production personnel develop customized procedures for blending in consultation with our customers. Blenders are available in both carbon steel for technical grade products and stainless steel for food grade and other specialty applications. In addition, a wide variety of packaging options are available.
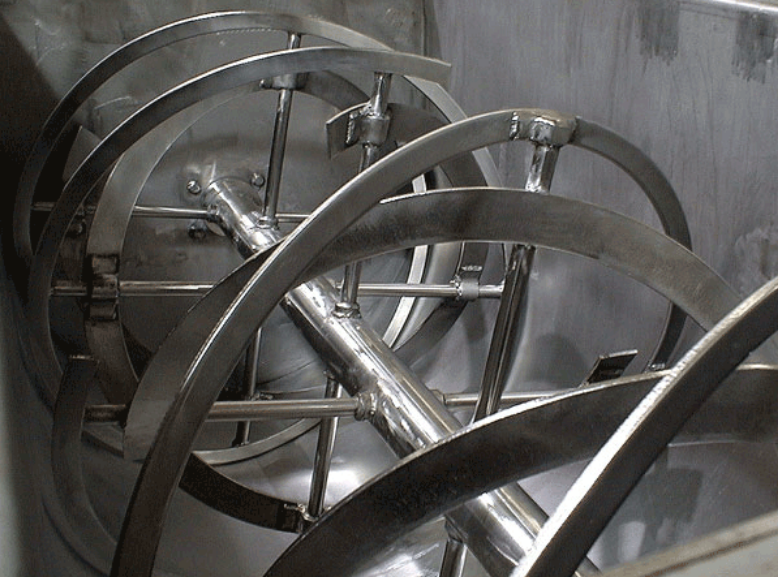
For blends that require more intense agitation, Fluid Energy has incorporated high speed choppers into our systems. During mixing, the ribbons continuously sweep product across the choppers for a high quality, more thorough mix. The rotating choppers impact the product at a high rate of speed. This added feature increases Fluid Energy’s capabilities to give customers a wider variety of blending options.